Like many areas of airfreight transportation and logistics, ULD transfer and repair are inundated with manual processes. The lack of digitization and reliance on paper forms, phone calls and manual data logging leads to negative outcomes from a lack of clarity into who is responsible for damages to equipment to misplaced or lost ULDs
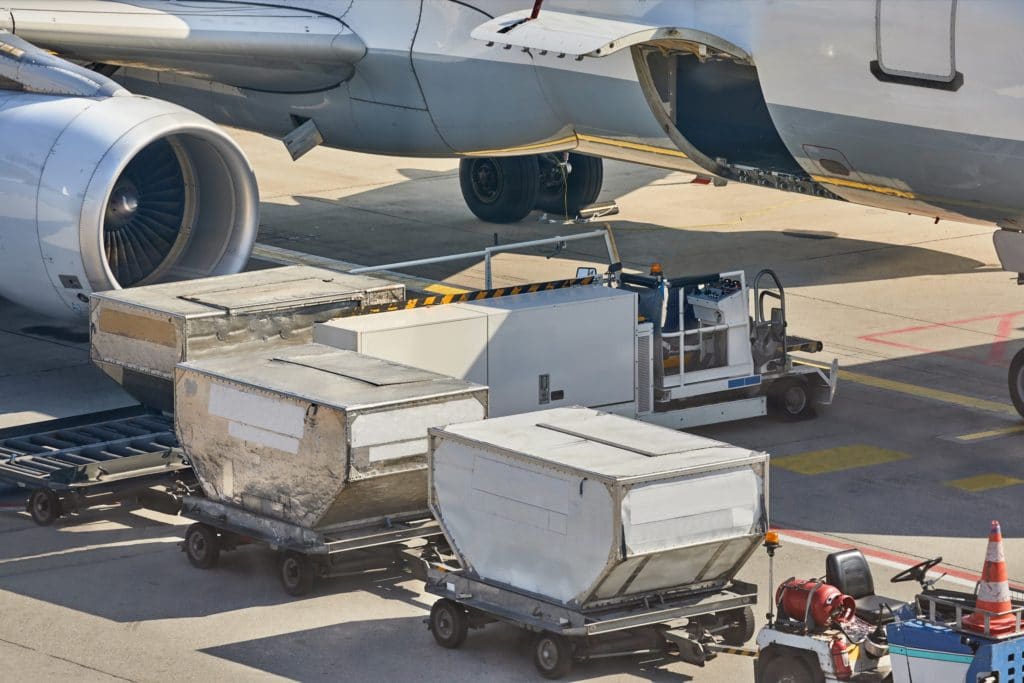
How do manual processes slow down ULD management?
During the COVID-19 pandemic, air cargo has been the bright spot for aviation, with e-commerce demand in particular growing rapidly. Work procedures at airports and with airlines have changed due to the pandemic, in many cases making manual processes more difficult. Data accessibility and keeping track of cargo and equipment can ease operational bottlenecks, which manual processes slow. With a mode as fast as airfreight, every day counts and when ULDs need repairs, faster access to information means significant improvements in ULD downtime.
Hong Kong-based engineering and ULD repair company Ground Support Engineering Ltd (GSEL) is trialing Virtual Control’s cloud solution and expects the technology to address some of its major pain points. One of the company’s major challenges involves the lack of visibility into the repairs needed, with no clarity into the number of damaged ULDs or the extent of the damage.
A secondary pain point relates to the inspections required for damaged containers by the Federal Aviation Administration, which must be completed by certified inspectors under FAR 145. With no visibility into the number of inspections needed or efficient method of recording the inspections, planning around inspections is a painstaking process that involves manual logging of containers and handwritten notes that are then transcribed into the computer system.
The manual logging process poses more challenges than the slow task of entering handwritten notes into a computer system, however. The nonprofit organization ULD CARE estimates that the airline industry spends roughly $300 million per year repairing ULDs, with a current lack of accountability due to an opaque transfer process. As the parties held responsible by regulatory authorities, airlines are primarily left with the repair bill.
Even when containers are undamaged, virtually every major airport has a yard full of ULDs, some of which fall out of manual systems as notes are lost or overlooked.
“The vast majority of transfers are airlines to third parties — ground handlers, freight forwarders, cargo terminals, and then cargo terminals to freight forwarders,” says Bob Rogers, vice president and treasurer of ULD Care. “This is where the visibility and the accountability of the whole thing drops off.”
With no easy way to locate these missing containers, asset management becomes difficult for ULD management companies and airlines. With a paper trail gone cold, determining responsibility through the chain of custody may be impossible.
What efficiencies are realized by digitizing ULD management?
Digitization eliminates or mitigates many of these concerns. Improved visibility into ULD transfers will help airlines, which bear the regulatory responsibility for ensuring ULDs are properly maintained, address problem areas in the handling process of GSPs and work toward reducing ULD damages and associated repair costs.
When repairs are needed, the ability to scan damaged ULDs and log damages into a system accessible to repair companies cuts down on repair time by allowing the firms to prepare and respond more quickly.
“If we have a better idea of the damage, we can confirm against spare parts in stock and which spare parts will have to be ordered to decrease the turnaround time,” potentially reducing turnaround time for ULD repairs by as much as 50%, says GSEL General Manager Dirk Scott.
The mandatory inspection process of every pallet and ULD during any handover process and change of custody is also made significantly easier thanks to digital processes. The automated data exchange with ULD stock management systems helps to get full transparency in real-time. With the damage identified before arrival at a repair facility, and the number of containers to be repaired already known, inspectors know roughly what to expect and can complete inspections more quickly. Efficiency is also improved on the administrative side, as inspectors scan containers digitally and make notes only once, in a digital format that is visible to all parties, allowing for more time in inspections and less time completing forms.
The digital logging of ULDs and the availability of trusted data across the entire ULD management process will support the entire air cargo ecosystem by creating a clear chain of custody and physically logging the location of ULDs upon scanning.